Cross-laminated timber (CLT) is an engineered wood product made from multiple layers of kiln-dried lumber glued together at right angles. CLT is ideal for large floor, ceiling and wall applications, it is durable and stable than ordinary wood.
CLT Manufacturing Process
We can break down the CLT manufacturing process into nine main steps. Each step depends on the next step. Therefore, the first step of the process must be done correctly. So, let’s look at the CLT manufacturing process..
1. Timber Harvesting and Debarking
Harvesting and debarking (The process of removing bark is called debarking.) In this process, mature trees are selected from the forest. Primarily, spruce is used to make CLT, but it may also include some percentage of pine or larch and possibly hardwood.
In this process, the log is passed through a machine’s roller, consisting of several granular blade belts that clean the bark from the wood log.
2. Drying
The drying process is used to reduce the moisture content of the wood. Wood expands with moisture and contracts when dry. No customer likes wood that may shrink as it dries, compromising the structural integrity of the application.
A drying kiln is used. The kiln is a thermally insulated chamber that controls the temperature to facilitate complete wood drying.
3. Lumber Grouping
The grouping process ensures that different categories of wood are grouped based on wood quality, size, structural properties and knots. This process also determines the price of CLT grade. Lumber with superior structural properties is used for interior application purposes.
4. Cutting and Grinding
In this process, boards are made by cutting large logs. The surface of the wood must be smoothed after cutting before proceeding to the next step. To make it smooth, a grinding machine with sandpaper is used.
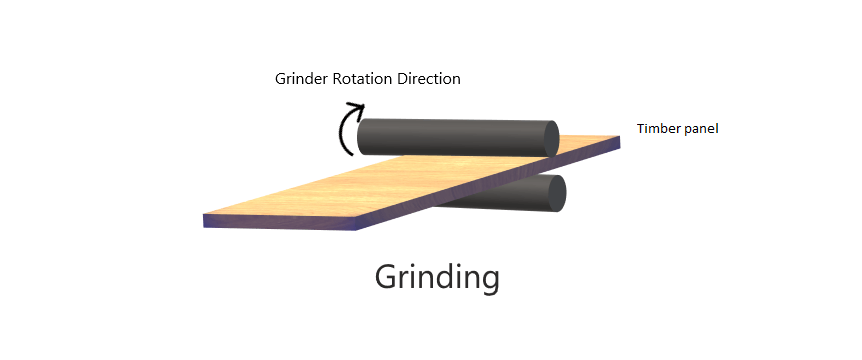
5. Adhesive Process
In this process, a waterproof adhesive is applied to the boards by nozzle spray. Polyurethane adhesives (PUR) or phenol resorcinol formaldehyde (PRF) are primarily used for CLT, finger joints, glulam and laminated logs.
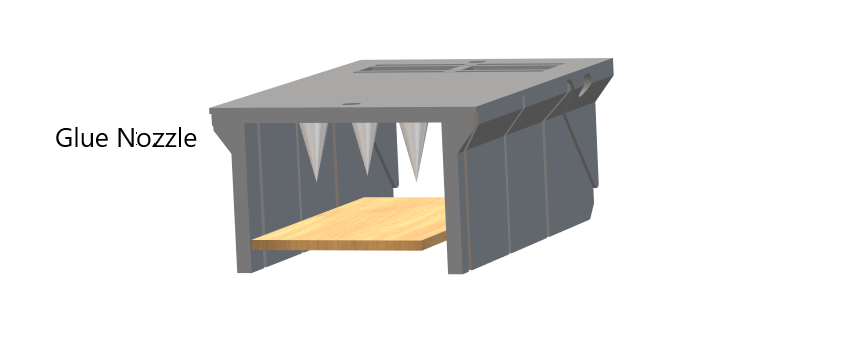
6. Panel lay-up
In this process, wooden boards (usually three, five or seven) are glued together at a 90 degree angle. Generally each board has a similar thickness (ranging from 17 mm to 45 mm).
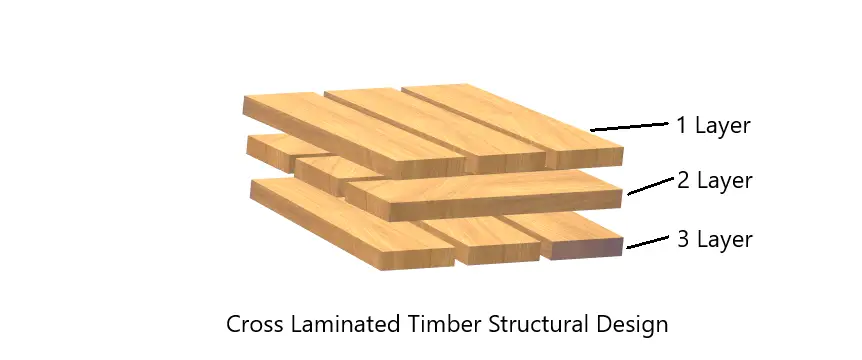
7. Heat and Pressure Process
CLT panels are pressurized at a high temperature. So that all the boards are glued to each other well. CLT structure has to bear a lot of load. So, all the panels must be firmly glued.
Temperatures of 100–150 °C and pressures of approximately 700–6000 psi are used for this process.
8. Cutting to CLT panel
The cross-laminated wood panel is almost complete but still not ready for production. In this process, it is cut into the right shape and size.
9. Marketing and Shipping
After cutting and finishing, CLT panels are ready for production and construction use. The finished CLT panel reaches the CLT store from the manufacturing production house at this stage. Now, customers can purchase CLT from local stores as per their requirements.